PROCESSING APPLICATION
Hold tight! We’re comparing your resume to the job requirements…
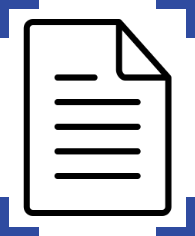
ARE YOU SURE YOU WANT TO APPLY TO THIS JOB?
Based on your Resume, it doesn't look like you meet the requirements from the employer. You can still apply if you think you’re a fit.
Job Requirements of Maintenance Manager:
-
Employment Type:
Full-Time
-
Location:
Baytown, TX (Onsite)
Do you meet the requirements for this job?
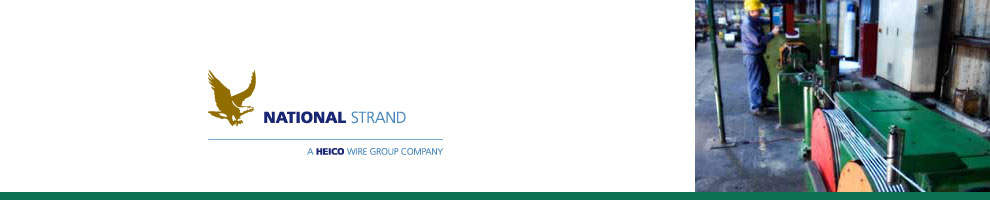
Maintenance Manager
The Company
National Strand is part of the Metals Processing Group which produces steel wire and cable/wire-related products that serve many industries and is wholly owned by The Heico Companies, LLC. The independent business model fosters entrepreneurship and growth and allows professional development at all levels.
Heico has a history of success. Since its founding over 40 years ago, The Heico Companies has grown from a single business to over 78 separate companies through a strategic acquisition policy, and by reinvesting its earnings into internal growth and new prospects. Historically talented at restoring distressed companies, Heico strategically targets acquisitions that will complement its ever-growing portfolio of companies in manufacturing, construction, and industrial services.
These four core operations are organized into groups: Applied Solutions Group, Construction Solutions Group, Industrial Technologies Group, and Metal Processing Group. Once acquired, new Heico companies are assigned to a group and run on a stand-alone basis, allowing for great independence as well as the opportunity to share knowledge about markets, production processes, and management practices across other Heico groups and companies.
Heico continues to seek out new opportunities and maintain its standard of success. The Heico Companies has remained a privately held company since its creation and maintains a majority ownership in each of its operations, which generates more than $3.3 billion dollars in revenues. Many of our businesses are certified Woman-owned Business Enterprises (WBE).
More information about the overall organization can be found at
.Job Description
- Ensuring the best practices to operate the machinery safely.
- Directs workers in electrical, electronic, mechanical, hydraulic, and pneumatic maintenance and repair of machinery and equipment.
- Assists workers in diagnosing malfunctions in machinery and equipment.
- Directs workers engaged in dismantling, assembling, and installing industrial machinery.
- Develop program to procure, organize and maintain recommended spare parts Ensure all maintenance work is properly tracked and documented in the CMMS system.
- Develop and implement a PM system to improve machine uptime.
- Studies production schedules and estimates worker hour requirements for completion of mechanical and electrical job assignment.
- Interprets company policies to workers and enforces safety regulations.
- Interprets specifications, blueprints, and job orders to workers, and assigns duties.
- Establishes or adjusts work procedures to meet production schedules.
- Recommends measures to improve production methods, equipment performance, and quality of product.
- Suggests changes in working conditions and use of equipment to increase efficiency of shop, department, or work crew.
- Analyzes and resolves work problems or assists workers in solving work problems.
- Initiates or suggests plans to motivate workers to achieve work goals.
- Preparation of maintenance budget for including major expense planning, emergency and routine maintenance, preventive maintenance, and machine lubrication, to ensure achievement of budget goals through regular review and reporting.
- All other duties as assigned.
Job Requirements
Competency: To perform the job successfully, an individual should demonstrate the following competencies.
- Problem Solving – Identifies and resolves problems in a timely manner
- Project Management – Completes projects on time and budget
- Oral Communication – Speaks clearly and persuasively in positive or negative situations
- Written Communication – Writes clearly and informatively
- Change Management – Develops workable implementation plans
- Business Acumen – Understands business implications of decisions
- Cost Consciousness – Works within approved budget
- Innovation – Displays original thinking and creativity
- Safety and Security – Observes safety and security procedures
Qualifications: To perform this job successfully, an individual must be able to perform each essential duty satisfactorily. The requirements listed below are representative of the knowledge, skill, and/or ability required. Reasonable accommodations may be made to enable individuals with disabilities to perform the essential functions.
Education/Experience: Bachelor’s degree from a college or university program; or four (4) to ten (10) years related experience and/or training; or equivalent combination of education and experience. Bachelor’s degree in mechanical/Electrical Engineering, a plus.
Language Ability: Ability to read, analyze, and interpret general business periodicals, professional journals, technical procedures, or governmental regulations; Ability to write reports, business correspondence, and procedure manuals; Ability to effectively present information and respond to questions from groups of managers, clients, customers, and the general public.
Math Ability: Ability to work with mathematical concepts such as probability and statistical inference, and fundamentals of plane and solid geometry and trigonometry; Ability to apply concepts such as fractions, percentages, ratios, and proportions to practical situations.
Reasoning Ability: Ability to solve practical problems and deal with a variety of concrete variables in situations where only limited standardization exists; Ability to interpret a variety of instructions furnished in written, oral, diagram, or schedule form.
Computer Skills: To perform this job successfully, an individual should have knowledge of Word Processing software; Spreadsheet software; Inventory software; Project Management software; CMMS software and Manufacturing software.
Certificates and Licenses: None Required – OSHA 30 hour recommended.
Supervisory Responsibilities: Directly supervises employees in the Maintenance Department; Carries out supervisory responsibilities in accordance with the organization’s policies and applicable laws; Responsibilities include interviewing, hiring, and training employees; planning, assigning, and directing work; appraising performance; rewarding and disciplining employees; addressing complaints and resolving problems.
Work Environment: The work environment characteristics described here are representative of those an employee encounters while performing the essential functions of this job. Reasonable accommodations may be made to enable individuals with disabilities to perform the essential functions.
Physical Requirements - The physical demands described here are representative of those that must be met by the Maintenance Manager position to successfully perform the essential functions of this job. Reasonable accommodations may be made to enable individuals with disabilities to perform the essential functions.
While performing the duties of this job, the employee is regularly required to sit and talk or hear. The employee is frequently required to stand and walk. The employee is occasionally required to use hands to finger, handle or feel and reach with hands and arms, lift and/or carry up to 50 pounds, balance, bend, stoop or kneel, climb, push/pull and squat, or crouch.